Ever wondered which machines create those ropes with unique textures? Well, you’re not alone! Many people are curious about the manufacturing process behind these versatile cords. So, let’s delve into the world of rope-making machinery and explore the diverse techniques used to produce a variety of textured ropes.
The world of rope manufacturing encompasses an array of specialized machines, each tailored to produce ropes with distinct textures and characteristics. Let’s unravel the mysteries behind these machines and discover their roles in crafting ropes of various textures:
1. Rope Knitting Machines
Knitting rope machines excel at producing ropes with consistent patterns, primarily distinguished by their round, flat, or elastic & non-elastic forms.
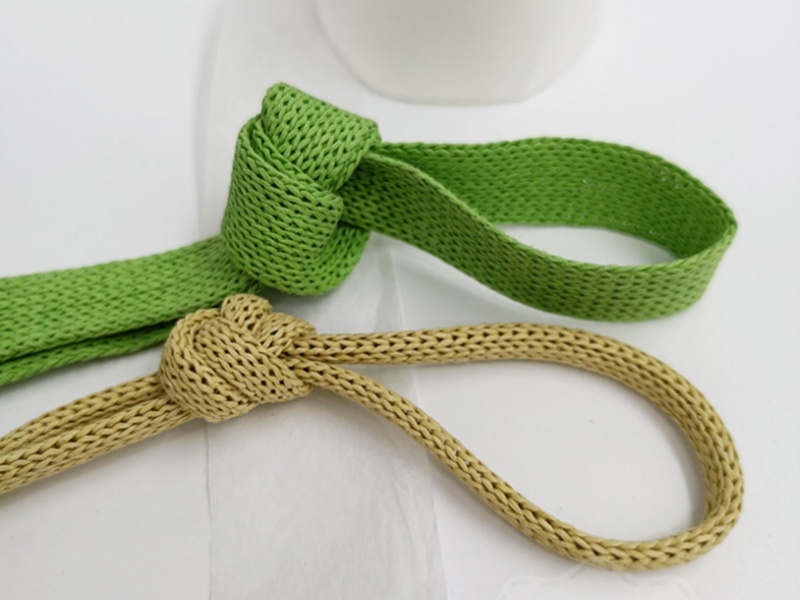
Needle Selection:
Needle selection aligns with yarn specifications, ensuring compatibility. Needle compatibility across different models is limited due to variations in hook size, length, and thickness. Switching needles with significant size differences typically requires a dedicated machine head.
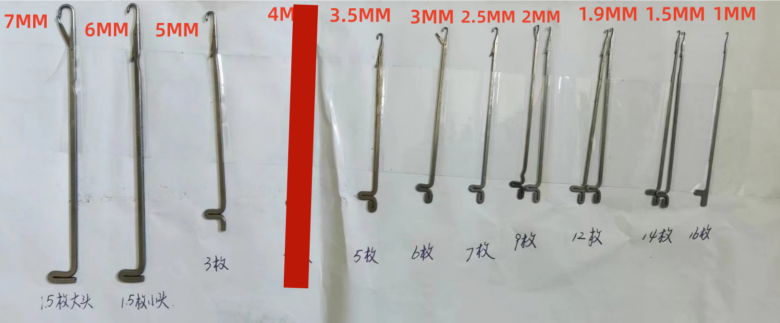
Needle Quantity:
Needle quantity is determined by desired rope density.
Spindle Core Diameter:
This is one of the most important figures in head customisation and determines the size of the rope.
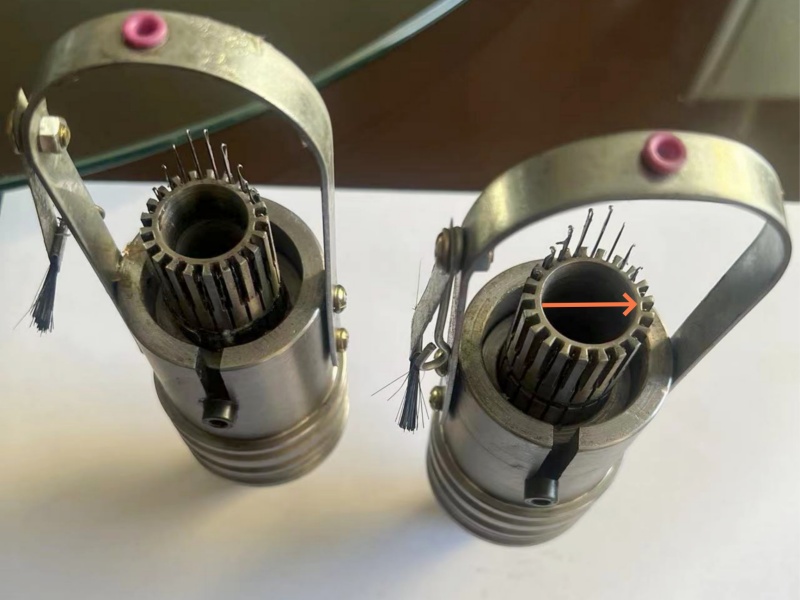
These machines typically produce single or two-colored ropes, with optional core filling capabilities.
Ropes produced by these machines find extensive use in various industries, including:garment and footwear, securing and bundling items, crafting fishing nets, and industrial applications.
The elasticated ear cords for the masks are usually produced by this machine.
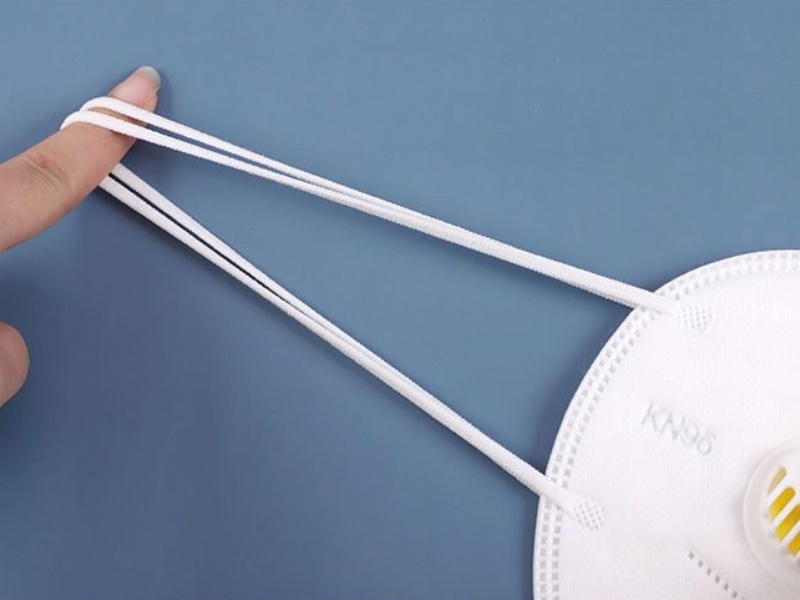
Advantages:
Customization Ease: Facilitates tailored rope designs
Cost-Effectiveness: Offers a budget-friendly solution
2. Fency Cord Cylinder Knitting Machines
Fancy cylinder knitting machines, also known as patterned knitting machines, elevate the art of knitting by introducing a realm of intricate designs and patterns. These machines, equipped with an array of needles and sophisticated programming capabilities, transform ordinary yarn into mesmerizing masterpieces.
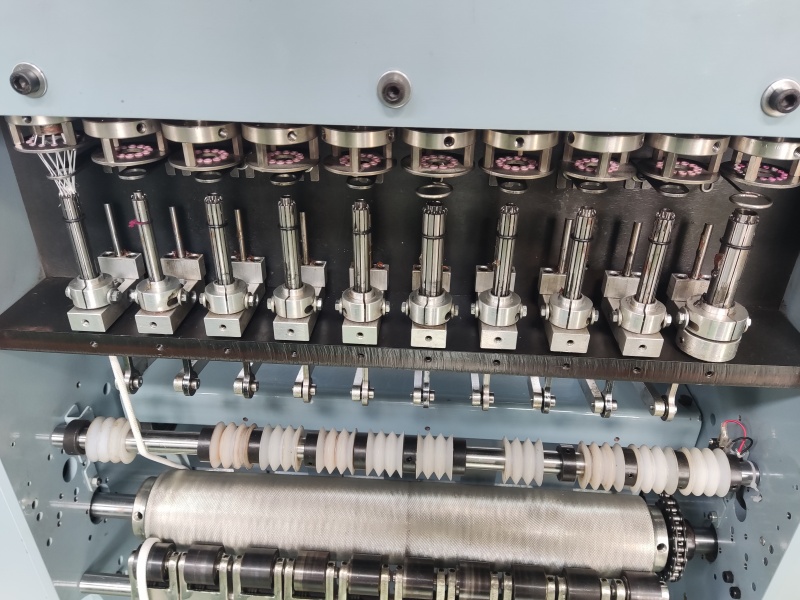
Fancy cylinder knitting machines, also known as patterned knitting machines, elevate the art of knitting by introducing a realm of intricate designs and patterns. These machines, equipped with an array of needles and sophisticated programming capabilities, transform ordinary yarn into mesmerizing masterpieces.
Needlework Versatility
Fancy Cylinders are often equipped with a wide selection of stitches to knit different patterns, motifs and textures.
Programmability
Some advanced fancy cylinder machines can be programmed or use specific knitting software to design and control the pattern and sequence of knitting.
Material adaptability
A variety of fibre materials, such as silk, wool and cotton threads, can be used to knit different items such as clothing, accessories and home furnishings.
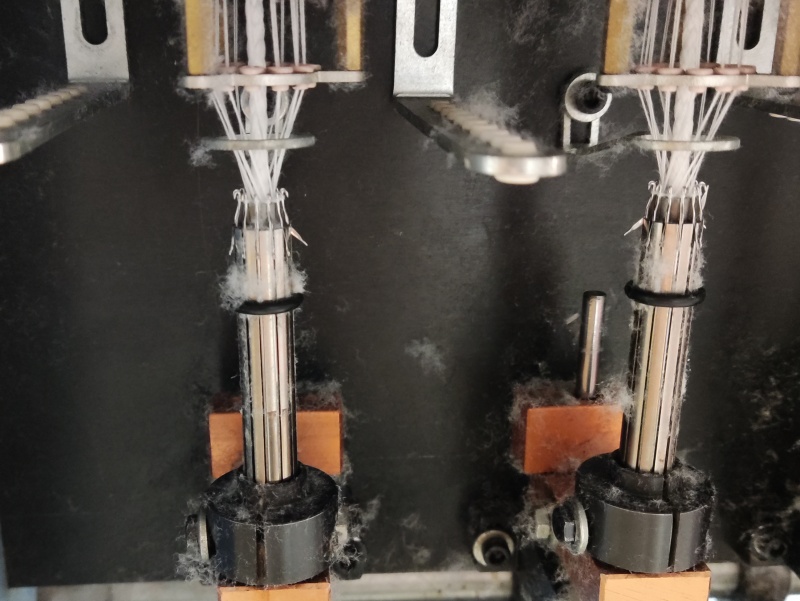
Creativity and personalisation
Fancy Cylinder Machine provides knitters with more room for creativity and can produce unique knitted items according to personal preferences and design needs.
Of course these machines can also produce single or 2-ply ropes. Currently the most widely used is still in the field of clothing, shoes and hats. Below are some pictures of single and double ply ropes produced on machines with different needle counts.
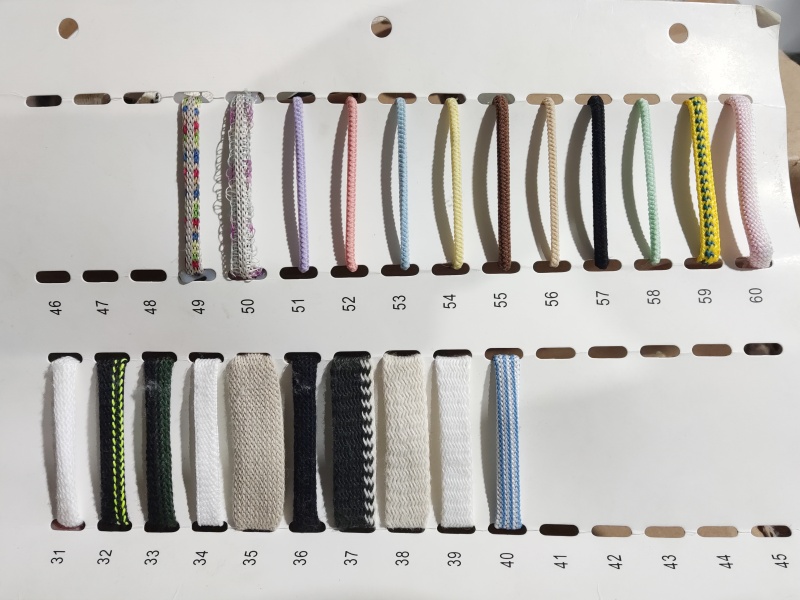
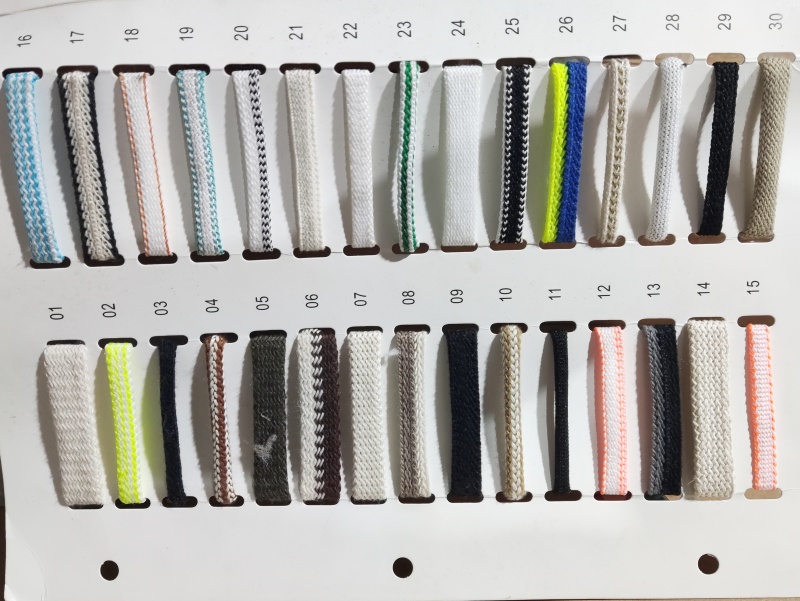
3. Rope Braiding Machines
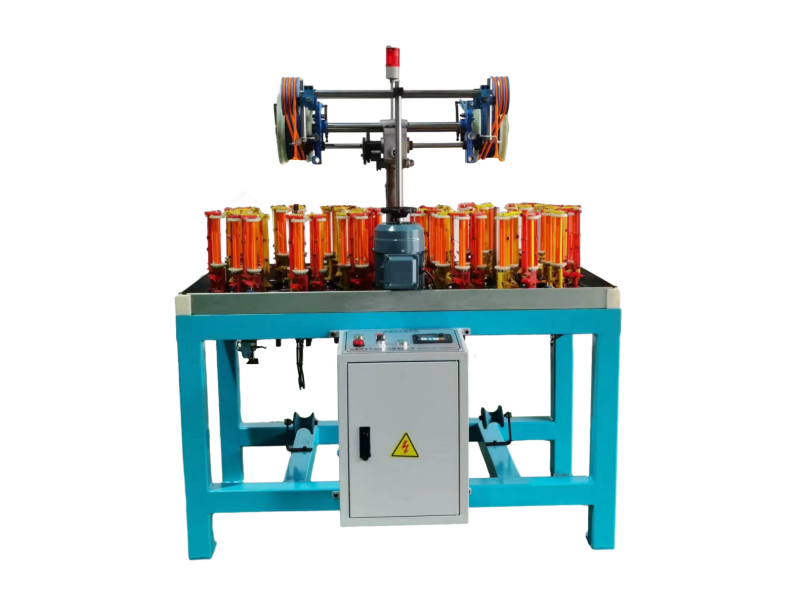
These ingenious machines intertwine multiple strands of yarn or fibers, resulting in intricate braided ropes. The pattern and texture of the braid depend on the number of strands and their interlacing arrangement.
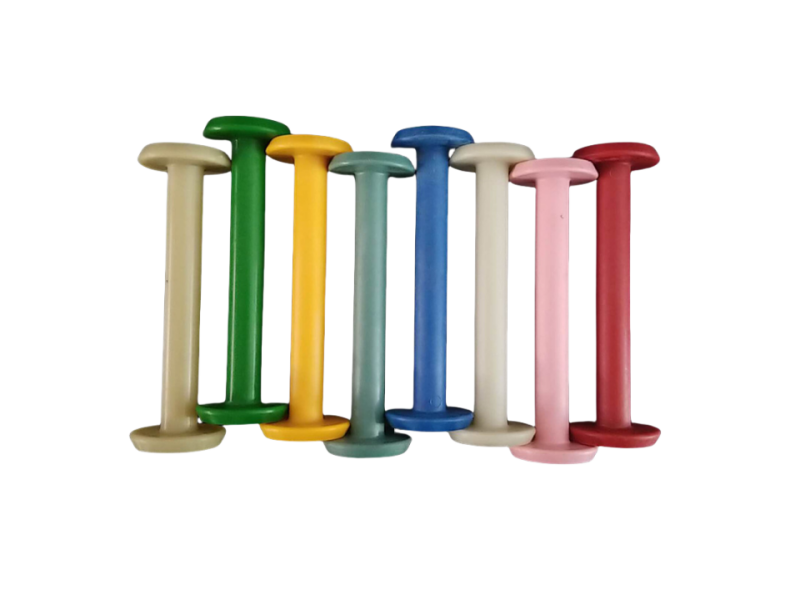
Spindles: The Key to Weaving Machine Versatility
In the world of weaving machines, spindles play a crucial role in determining the machine’s capabilities and applications. The number of spindles, which are the vertical rods that hold the yarn during the weaving process, directly influences the number of yarns that can be woven simultaneously.
16-spindle, 32-spindle, and 48-spindle weaving machines are differentiated primarily by their capacity for simultaneous yarn handling.
More spindles, more possibilities:
Higher spindle count: Enables weaving with more yarns, leading to:
Complex weaving structures and patterns
Enhanced production efficiency
Greater product diversity
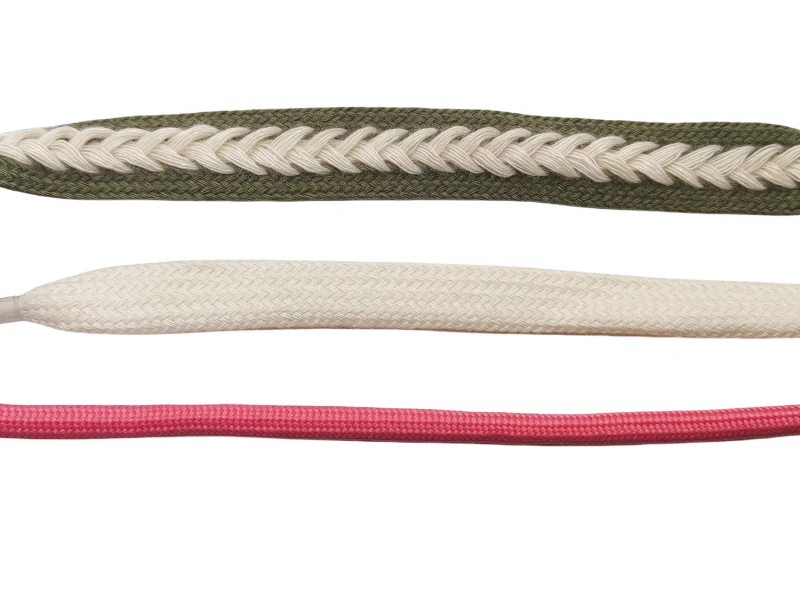
Application versatility:
Ideal for: Large-scale production,Complex patterns,High-quality requirements
Examples: Shoelaces,Elastic bands, Safety ropes,Pet Cords, Cable protection cords
Lower spindle count weaving machines:
Suitable for:
Relatively simple woven products
Small-batch production
Examples: Lucky bracelets, Fishing cord, Packing rope.
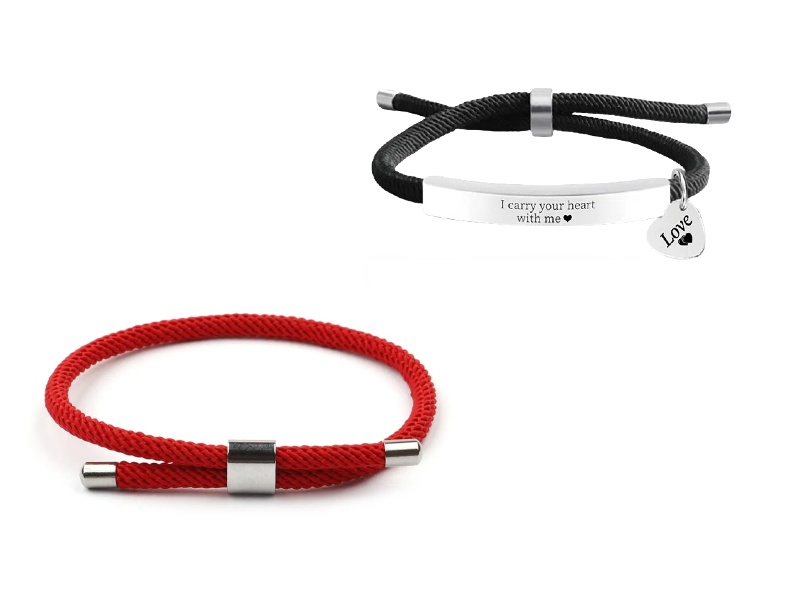
Please also consider in brand and model differences:
Specific performance and features may vary across brands and models.
Before purchase, you should consider:
1.Specific production needs
2.Product type
3.Budget
If you don’t know how to choose, let us know. Our team will help you make the right decision!
4. Rope Twisting Machines
A cord twisting machine is a mechanical device used to make rope by twisting multiple strands of yarn or rope into one strand to make it stronger and more durable. The direction and angle of the winding mdetermine the twist and strength of the rope.

The rope-making process typically involves three steps:
A. Combining multiple strands of yarn into a single strand of thick yarn
This step involves bringing together multiple strands of individual yarns and twisting them together to form a thicker, more robust strand. The number of strands used will influence the overall thickness and strength of the resulting rope.
B. Twisting multiple strands of thick yarn into a rope
In this step, several strands of the thick yarn produced in the previous step are further twisted together, but in a different direction compared to the initial twisting of individual yarns. This creates a rope with a specific lay, which affects its handling characteristics, strength, and resistance to abrasion .
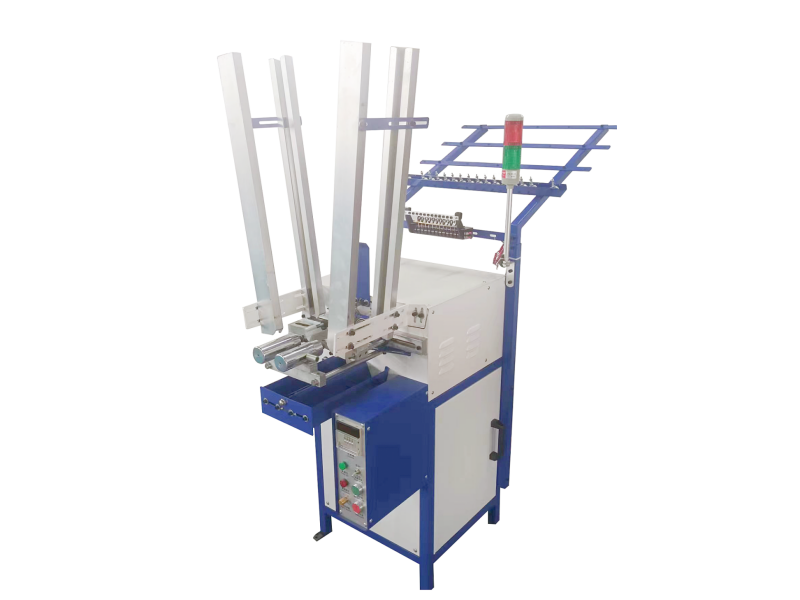
C. Coiling and packaging the rope according to desired specifications
The final step involves coiling or spooling the finished rope in a neat and organized manner, ensuring it is properly packaged for storage or transportation. The coiling method and packaging materials used will depend on the intended use of the rope and the desired presentation.
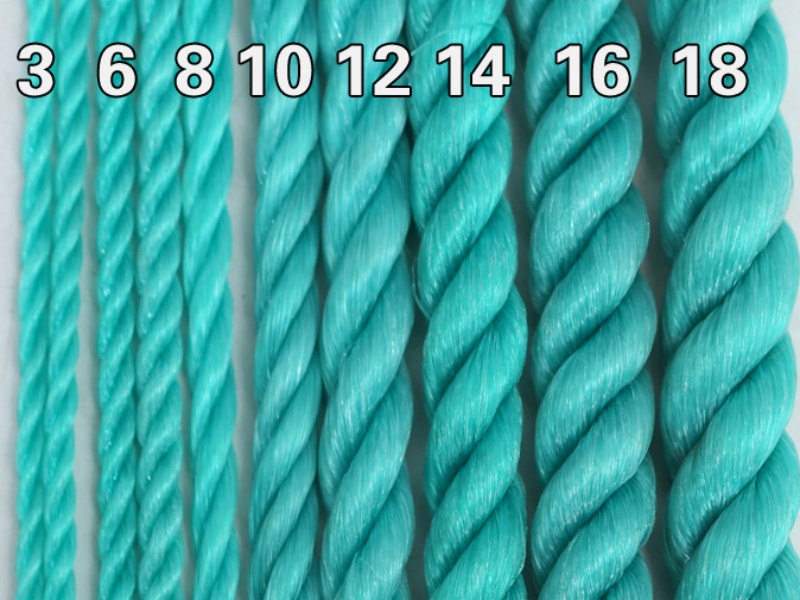
The most common rope-making machines are three-strand rope-making machines, but there are also two-strand, four-strand, and even multi-strand rope-making machines.
Twisting machine have a wide range of applications, including:
Construction: Used to make scaffolding ropes, sling ropes, safety ropes, etc.
Fishing: Used to make fishing nets, fishing ropes, etc.
Agriculture: Used to make binding ropes, tow ropes, etc.
Transportation: Used to make cables, slings, etc.
Sports goods: Used to make skipping ropes, climbing ropes, etc.
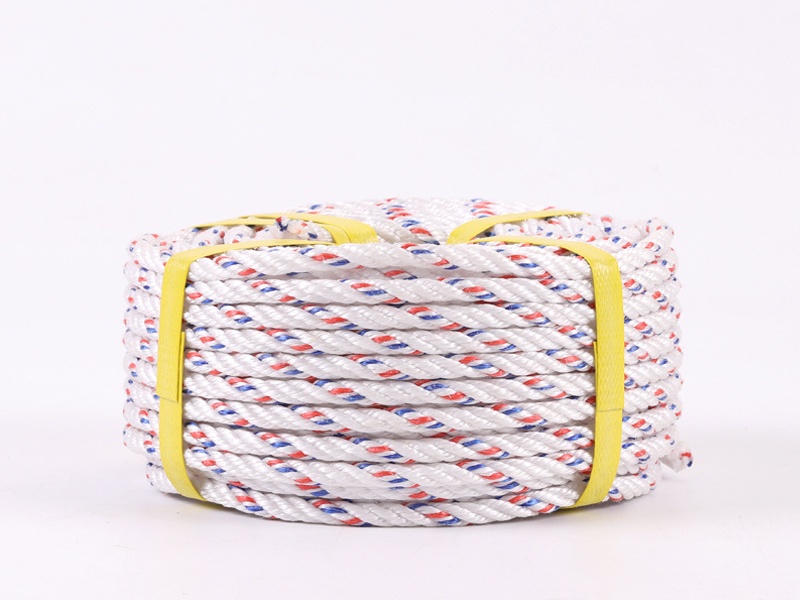
Conclusion
In conclusion, rope making machines play a vital role in a wide range of industries, from the textile industry, construction and agriculture to fishing and transport. They are indispensable in a wide range of applications because of their ability to transform a single yarn into a strong and durable rope with specific characteristics.
As technology has advanced, rope making machines have become more sophisticated, increasing productivity, precision and versatility. The four main types of rope making machines – are available to meet a variety of production needs and rope characteristics.

As you delve into the world of rope making machines, you’ll discover a fascinating combination of engineering principles, materials science and practical applications. Whether you’re a seasoned professional or just beginning to explore the field, we encourage you to seek guidance and support from our team-MIIYOUNG. We are committed to helping you make informed decisions and select the ideal rope making machine for your specific requirements.